Part Number: | MST360D-0012-FT-N0CN-NNNN |
---|---|
Manufacturer: | Bosch Rexroth Indramat |
Series: | MST Synchronous Torque Motor Series |
- Straightforward Pricing: No Rush Fees, No Credit Card Fees
- MPN: R911309734
- Call for Expedited Shipping and Product Condition Options



The MST360D-0012-FT-N0CN-NNNN Synchronous Torque Motor comes equipped with Winding type 0012 and cools down through the use of Liquid Cooling. The motor's frame length is D, which is correspondent to the amount of torque (The higher the length, the more torque. The IndraDyn T motors are always fitted with a stator-cooling jacket foroperation with liquid cooling.
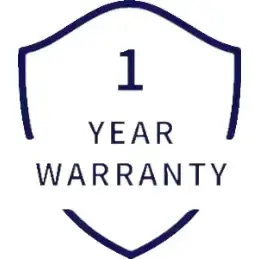
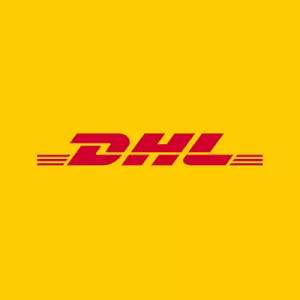
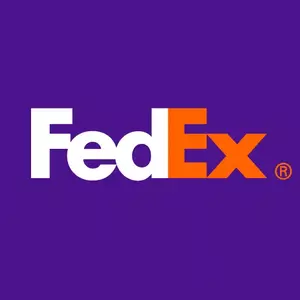
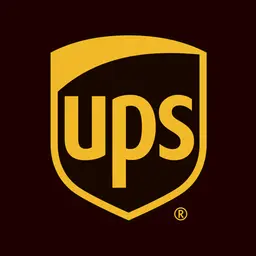
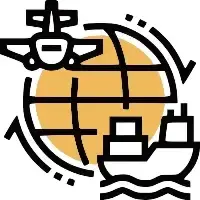
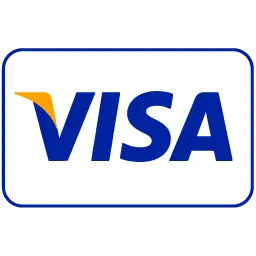
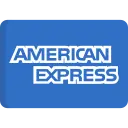
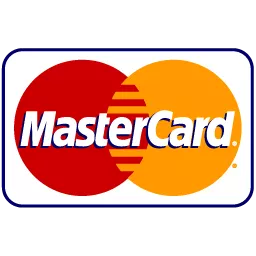
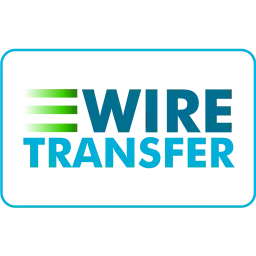