3 Benefits of Lean Manufacturing
24 April, 2019
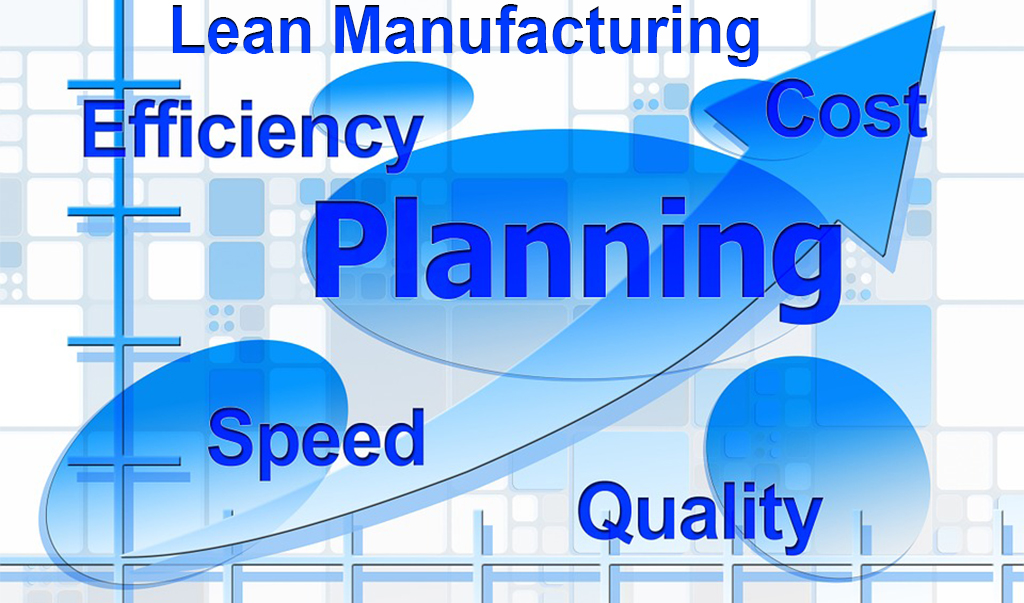
We All Want More Value Out of Day
If you are someone who wants to improve your workday, then Lean Manufacturing can empower you to make lasting impact. Improvement, by definition, requires change, and it is often intimidating to know where to start. Lean Manufacturing provides a framework to identify improvements and systematically achieve them. Over the last 20 years of my career, in multiple industries, I have found the principles of Lean Manufacturing to be critical to my success.
Conversations about Lean Manufacturing (also called ‘Lean Sig Sigma’ or just ‘Lean’) can be full of jargon and confusing foreign terms. But, at the core, Lean is simply about continuously removing the wasteful activities in daily routine and improving upon the quality of results. While these principles have taken hold in manufacturing circles, every business can benefit from them.
Take a few moments to think about your last week of work. Has it been filled with non-stop valuable experiences? Were the results at the level of quality you wanted? Chances are, if you are like most people, a significant percentage of your day was spend doing things that slowed you down or prevented you from delivering the quality of results you desired.
But we can’t just find more hours in the day. In order to achieve better results we must spend less time doing things that don’t add value to our goals. This is easy to say, but hard to do. Here are 3 critical Lean skills (in the order that I learned them) that have helped me in every workplace I have been a part of:
- Learn how to identify wasteful activities
- Truly understand the processes & challenges
- Collect data and drive all decision making from it
Learn how to identify wasteful activities
It
can be harder than you think to identify waste. We can all fall prey to
accepting the status-quo. To help with this, Lean categorizes waste and makes
it easier to spot. Currently, there are 8 main forms of waste identified by
Lean. These can be remembered by using the mnemonic DOWNTIME. Take a look at
the graphic below, and then think about your day. Do any of these apply?
(Spoiler alert: They will)
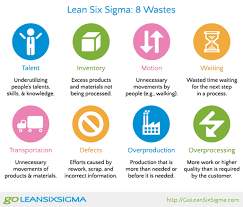
Learning how to “see” this waste is the first major step in your Lean journey. It was difficult at first for me to think this way, but now it is almost instinctual. WARNING: Once you learn how to see waste, you will never be able to “unsee” it, so be prepared to have a life changing experience.
Truly Understand the Processes & Challenges
Once your eyes have been opened to the waste around you, it can be tempting to just start changing things to make them “better”. I learned the hard way (through a number of failures) that I had to first seek to understand my current state before making attempts at improving it. Would you want somebody changing around your workday without understanding what you do? Neither did my co-workers.
To truly distinguish yourself as a top-notch Lean champion, take the time to deeply learn a process. People around you will notice the difference, feel appreciated, and be more prone to partner in your proposed changes. Some great tools for this are:
- Process maps: Defines the steps of the process and who owns them
- Strap yourself to the part: This is one of my favorites. Pick an item (like a manufactured component) and follow it through its entire life-cycle. You will be amazed at what you discover
- Cause and Effect diagrams: A great way to collect information on a challenge and link it to a number of possible sources
Collect your data and make your decisions based on it
Once
I had found waste, and understood my process, it was time to inform others and
start collaborating around change. My experience has been that few people
naturally let data drive their decision making. We usually want to go after
whatever is currently causing the most angst.
It was critical that I learned how to collect important data (raw numbers or facts) and turn it into information (insights that can guide effective decision making). There are countless ways to collect & display data, but the following are methods that ALWAYS seem to land with every audience:
- Data Collection – Checksheets: This tried and true method is a simple way, for even the least technically-inclined person, to collect information about a process. They can be provided via hardcopy, or softcopy, depending on what works best for your environment.
- Data Display – Histogram: No matter the audience, we all understand that we need to go after the “big bars”. Histograms help us set clear priorities and create the largest return for an investment.
Conclusion
These are the tools that have helped me in large Fortune 500 companies (Raytheon), non-profit healthcare (Valley Children’s Hospital), and even consulting for small local CA businesses (like Pike Pool
- Spa). Lean reduces cost, increases efficiency, and vastly improves employee satisfaction. Give one of these tools a try this week, you will not be disappointed. For more ideas, you can check out the reference below!
- Call: 1-888-551-3082
- International: 1-919-443-0207
- Fax: 1-919-867-6204
- Email: sales@wakeindustrial.com
- Address:
- 1620 Old Apex Rd
- Cary, NC 27513